Tool Construction
b-plastic’s own tool construction is a core element in the process chain of our plastic injection molding production and a decisive advantage for our customers.
Whether for the manufacture of products from our standard range or, in particular, customised products, our own on-site toolmaking guarantees maximum flexibility as well as sustainable and consistent quality and productivity from a single source thanks to its close “process interlocking”. This is an outstanding advantage, e.g. compared to tool production outsourced to Asia, which is detached from the rest of the process chain.
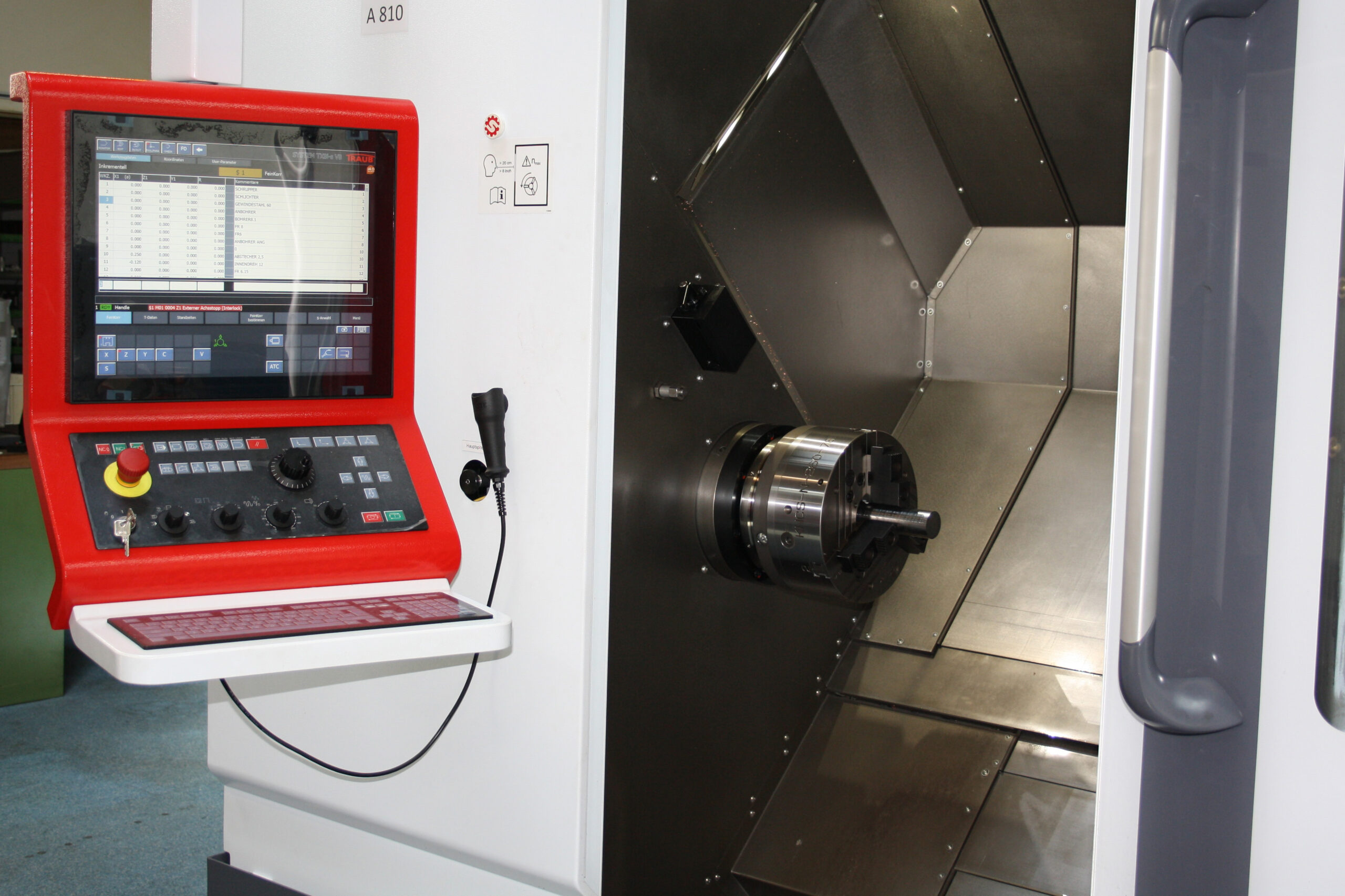
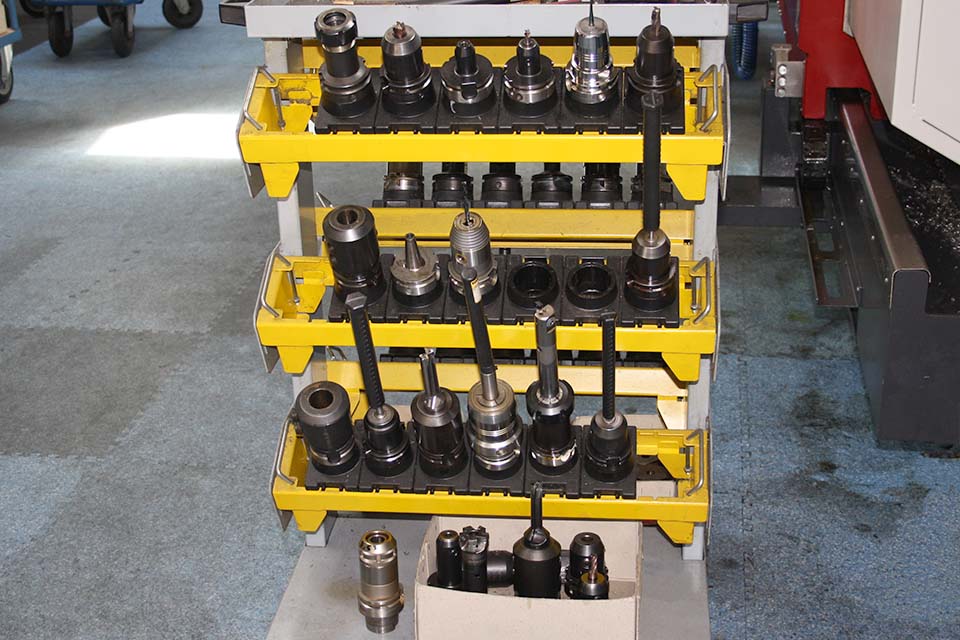
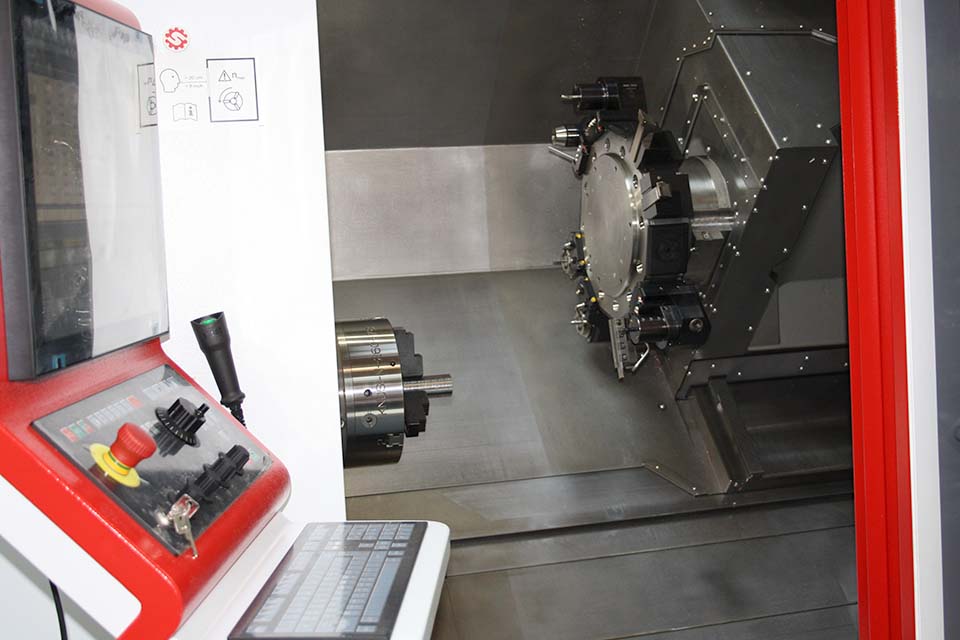
The basis for the development of toolmaking is, on the one hand, the dynamic process of internal exchange of experience and knowledge between our
- Toolmakers,
- process mechanics,
- developers, designers and our
- quality department
which is also flanked by ongoing education and training.
On the other hand, our own technical standards are enriched by “external know-how” through continuous communication with our partners and suppliers, among others, in order to constantly improve and optimise them.
In addition to high qualifications, close-knit knowledge networking and intensive teamwork, the technical equipment plays an essential role in ensuring high process reliability, product quality and productivity for our customers.
Our development systems, control systems and machine tools are also closely “wired” together to ensure a seamless and productive exchange of information and consistently high quality. We manufacture on modern CNC machines in various processing categories.
Some technical features of the Tool and Apparatus Construction Department at a glance:
- CNC milling on 5-axis machining centres
- CNC turning on 4-axis universal lathes – centres
- Die-sinking EDM on CNC die-sinking EDM machines
- Die sinking on EDM drilling machines
- Direct data transfer from the CAD systems to the CAM system
- Subsequent data processing using CAM technology
- Direct data transfer from the CAM systems to the machine tools