Information about plastics
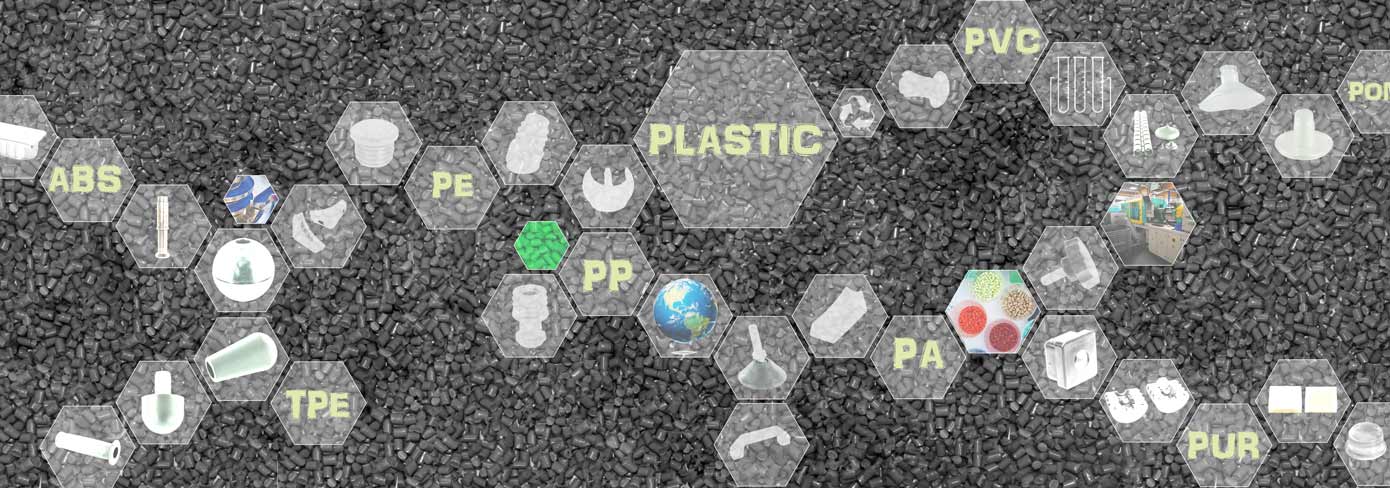
The first four datasheets below give a brief overview of the properties of the main plastics processed at b-plastic.
This is followed by a small glossary of other plastics, additives, compounds and many other interesting points relating to plastics.
This brief summary has been developed in discussions with our raw material suppliers and excludes any warranty or liability.
Mainly processed plastics at b-plastic
PA – polyamide
Physical – mechanical properties
Normal polyamide (1.07-1.14 g/cm³) is a medium-weight, semi-crystalline technical all-round thermoplastic. Polyamide has a relatively high water absorption (hygroscopic), which, depending on the type of polyamide and application, is adapted to the ambient climate in the factory by conditioning (warm water storage) the moulded parts, insofar as diffusion of the air humidity is not sufficient. Only …continue reading
PE – polyethylene
Physical – mechanical properties
0.90-0.96 g/cm³, PE is a very light semi-crystalline thermoplastic from the class of polyolefins, whereby VLD= Very Low Density ~0.90 g/cm³ and HD= High Density ~0.96 g/cm³ limit the density range. PE is water-repellent (hydrophobic) in normal settings like most polyolefins. PE is very tough. The modulus of elasticity, tensile strength and surface hardness give low values, increasing from VLD-PE to HD-PE. Good resistance to expansion cracking is predominantly found in VLD-PE and LLD/MLD-PE. With …continue reading
PP – polypropylene
Physical – mechanical properties
With 0.90-0.91 g/cm³, normal PP is a very light semi-crystalline thermoplastic from the class of polyolefins. PP has good toughness and excellent fatigue bending strength with suitably thin cross-sections. Compared to homopolymer PP, copolymer PP also has particularly good notched impact strength and is therefore also suitable for technical applications. The creep strength decreases sharply with increasing temperature. PP is water-repellent (hydrophobic), like most polyolefins. In terms …continue reading
PVC – polyvinyl chloride
Physical and mechanical properties
At 1.14-1.56 g/cm³, soft PVC is a relatively heavy amorphous thermoplastic, due to its halogen component (Cl). Depending on the plasticiser used, there are soft-rubber-like compounds of 40 Shore A (Shore A = hardness determination for soft plastics) to hard-rubber-like compounds of 98 Shore A. The latter corresponds roughly to the transition range …continue reading
Small glossary
For other thermoplastics, thermosets, thermoplastic elastomers, a brief explanation follows with the most important basic knowledge and properties of the plastics and terms described:
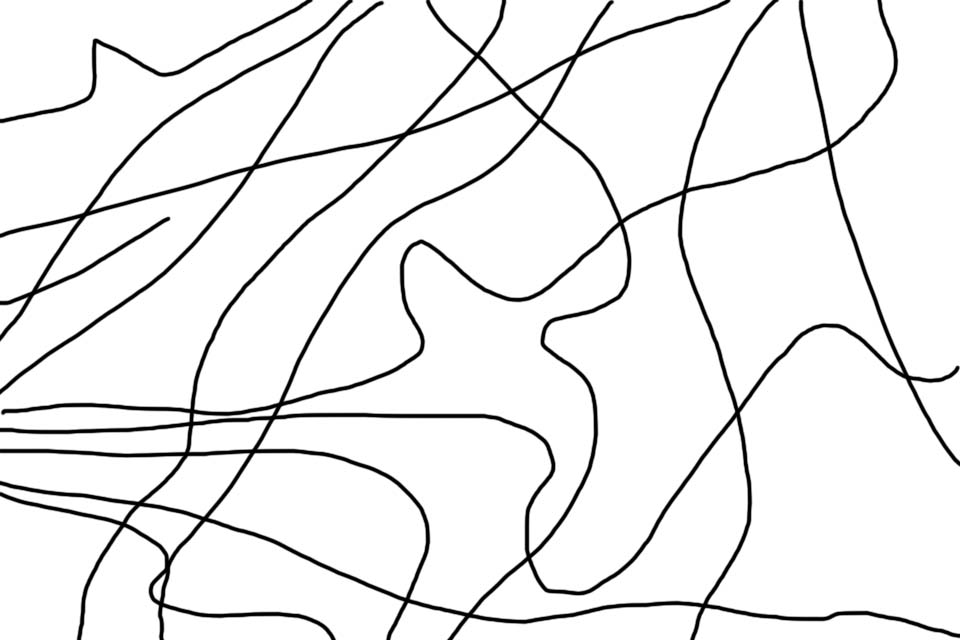
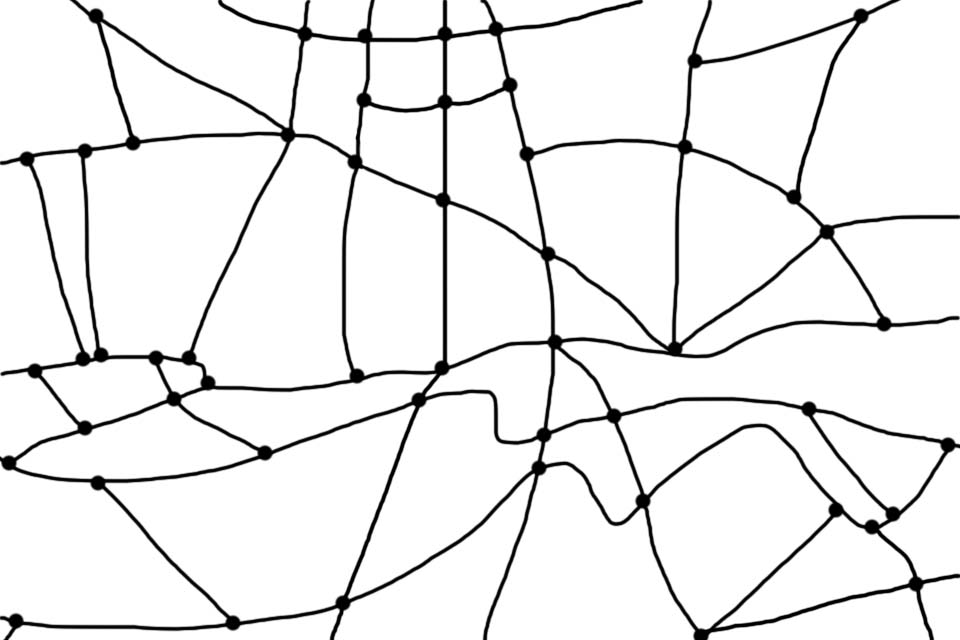
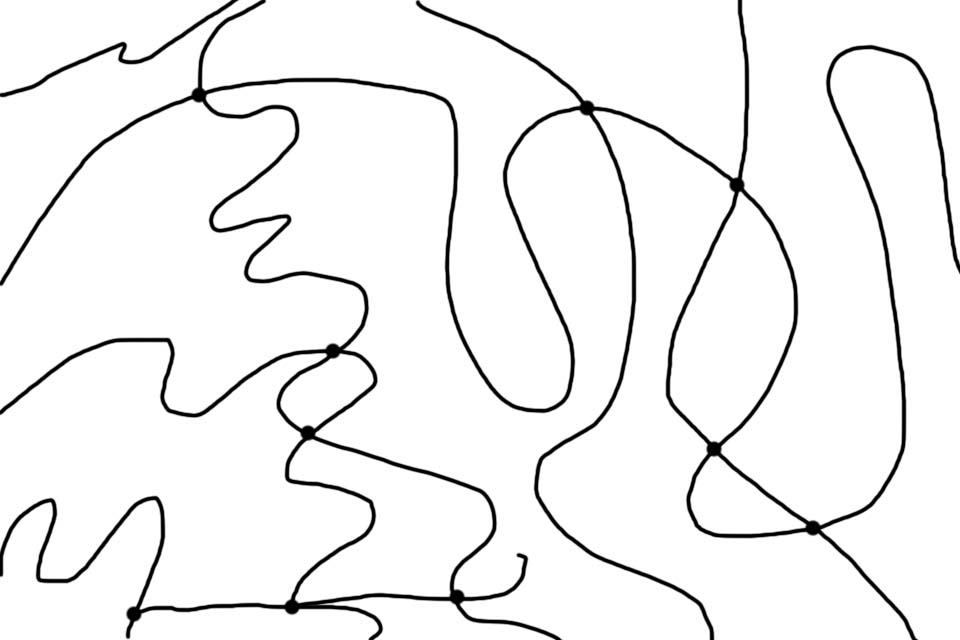
Collective term thermoplastic
Thermoplastics are normally hard or even brittle at room temperature. However, if they are heated within a certain temperature range, they become soft and plastic, as the loose, unconnected molecular chains can now move against each other more easily. When heated further, the molecular chains flow and the thermoplastic melts. Above the melting temperature, the thermoplastics gradually begin to decompose. In the presence of oxygen or open fire, the thermoplastic burns with an open flame or chars.
Thermoplastics are the largest group of synthetic polymers (=plastics) by volume. The four most important are listed below:
- Polyethylene
- Polypropylene
- Polystyrene
- Polyvinyl chloride
These four commodity plastics account for two-thirds of all plastic production. They surround us every day in the form of packaging, appliance housings and countless other everyday objects.
Collective term thermosets
The collective term thermosets (before processing and cross-linking of single or multi-component resins or powders) covers hard, non-plasticisable plastics with three-dimensional, close-meshed, cross-linked molecular chains, which can be divided into the following main types:
- Epoxy resins (EP)
- Urea-formaldehyde (UF)
- Melamine resins (melamine-formaldehyde = MF)
- (Methylmetha-)acrylate resins (MMA)
- Phenolic resins (phenol-formaldehyde = PF)
- Polyester resins (unsaturated polyester resins = UP)
- Cross-linked thermoplastics – by irradiation and/or addition of cross-linking agents – example: cross-linked PE (XLPE or PE-X) for water pipes and films to increase mechanical values, chemical resistance and continuous service temperature.
The different thermoset settings are numbered in a standardised way under the term Moulding Material (FS), e.g. FM31.
Collective term elastomers (also synthetic rubbers and elastoplastics)
The collective term Elastomers are soft, non-plasticisable plastics with three-dimensional, wide-meshed, cross-linked molecular chains, which can be divided into the following main types:
- Acrylic ester rubber (ACM, ANM, AR)
- Bromobutyl rubber (BIIR)
- Butyl rubber (GR-I, IIR)
- Chlorobutyl rubber (CIIR)
- Chlorosulphonated polyethylene (CSM)
- Epichlorohydrin rubber (CO, CHR, ECO, ETER)
- Ethylene propylene terpolymers (EPDM)
- Ethylene VAC copolymers (EVA,E/VA)
- Fluorine rubber (FPM, CFM, MFQ)
- Nitrile rubber (GR-N, NBR)
- Polybutadiene (BR)
- Polychloroprene, chloroprene rubber (CR)
- Polyisoprene, natural rubber (NK, NR)
- Polysulphide rubber (SR)
- Silicone rubber (SI)
- Styrene-butadiene rubber (GR-S, SBR)
- Urethane rubber (AU, EU)
Rubbers in liquid form are designated with an “L” in front of the abbreviation e.g. LBR. Mixtures of certain rubbers with each other in certain mixing ratios and with the addition of homogenisers or compatibilisers are possible to a very limited extent and sometimes with considerable effort and are usually offered by the raw material manufacturers in the chemical industry or by chemical specialists.
Collective term thermal elastomers – TPE (also elastoplastics)
Thermal elastomers is a collective term for thermoplastics with elastic properties similar to those of real elastomers (with cross-linked molecular chains: synthetic rubber, artificial rubber). These are then subdivided according to their similarity to the corresponding thermoplastics:
- TPA (TPE-A) = thermoplastic copolyamides
- TPE (TPE-E) = thermoplastic copolyesters
- TPO (TPE-O) = thermoplastic olefins (-> polyethylene, polypropylene)
- TPS (TPE-S) = thermoplastic styrene derivatives (-> polystyrene, styrene butadiene, ABS, ASA, etc.)
- TPU (TPE-PU) = thermoplastic urethanes (-> polyurethane) Resistance (non-binding)
- TPV (TPE-V) = thermoplastic vulcanisates (e.g. partially vulcanised EPDM)
These in turn differ from plastomers (with density < 0.9 g/cm³, very light elastomer-like thermoplastics with very short molecular chains – e.g. polyolefin plastomers [POPs]).
ABS – Acrylonitrile Butadiene Styrene
ABS (1.04-1.05 g/cm³) is a relatively light, amorphous engineering thermoplastic. ABS is relatively hard and stiff. It has a much higher toughness than the related high-impact polystyrene (SB). ABS has high thermal shock resistance and low water absorption (weakly hygroscopic). It has limited resistance to weathering. ABS is mainly used for high-gloss visible housings, multi-component injection moulded parts, chrome-plated parts and laser-marked parts. The inherent colour of standard grades is a highly opaque beige to yellowish brown. Crystal clear is available for special grades. ABS is processed at approx. 240-260 °C and ignites at approx. 400 °C with a bright sooty flame and a sweet odour.
- Look in our assortment under the category “plugs” e.g. the article series CGQ, CGQM, CGR, RJLM, RJLR, – category “caps” the article series KKASB, KKASG, PNA
NBR – Nitrile rubber
Nitrile rubber is a synthetic rubber. The abbreviation NBR is derived from Nitrile Butadiene Rubber. Nitrile rubber is made by copolymerising acrylonitrile (ACN) and 1,3-butadiene. Nitrile rubber vulcanisates have high resistance to oils, greases and hydrocarbons, good ageing properties and low abrasion. The thermal application range is between -30°C and +100°C, depending on the compound structure, and up to 130°C for short periods. The material cures at higher temperatures. The hardness of the material is between 60 and 80 Shore depending on the article.
- Have a look at the category “Machine and apparatus feet” in our assortment. Many article series, such as MFEA, are offered with rubber support surfaces for slip resistance.
PC – Polycarbonate
PC (1.2 g/cm³) is a medium weight, amorphous engineering thermoplastic. PC is very hard and has particularly high fracture toughness. PC is characterised by high heat resistance, low temperature dependence and low water absorption (weakly hygroscopic). PC is mainly used in the interior for highly transparent housings and covers, for highly break-resistant components and for optical components (CDs, DVDs, lamp components, lenses). The inherent colour is crystal clear. PC is processed at around 320-350°C and burns in the flame (extinguishes outside).
- Take a look at our product range under the heading “Control hardware” the article series DGA, DCA
POM – Polyoxymethylene (also acetal resin, para- and polyformaldehyde or polyacetal)
POM (1.42 g/cm³) is a relatively heavy, semi-crystalline engineering thermoplastic with the structure -(CH2-O-)n- for the homopolymer. Among non-reinforced thermoplastics, POM has very high strength and stiffness (even at high continuous loads and low temperatures), high dimensional stability and excellent fatigue resistance. Its wear resistance is almost as good as that of PA. POM is preferred for engineering applications such as snap-fits, bearings (also in combination with silicone or PTFE additives), rollers and gear components. The inherent colour of standard grades is opaque white. POM is processed at around 180-190°C, ignites at around 375°C and burns at 323°C with a slightly bluish flame and a pungent formaldehyde odour.
- Take a look at our product range under the heading “Connecting elements” the article series 137, heading “Cable management” the article series KBK18, KBK19, KBK20, KBK21 – heading “Inserts” the article series LBS1
PTFE – Polytetrafluoroethylene (trade names: Teflon – Dupont, Hostaflon, Dyneon, GoreTex)
PTFE (2.16 g/cm³) is a very heavy, semi-crystalline engineering thermoplastic with a Shore D hardness of 55-60. It has the structure CnF2n and belongs to the class of polyhaloolefins. Although PTFE is classified as a thermoplastic, due to its very narrow melting and decomposition temperatures, it can generally only be processed by sintering or pressure sintering and is therefore not subject to the degrees of freedom of most other thermoplastics.
It was discovered by Roy Plunkett in 1938 and patented by Dupont in 1941. PTFE tends to creep under pressure and may need to be stabilised with glass fibres or other strength additives. It is very inert. Even aggressive acids such as aqua regia will not attack PTFE.
PTFE has one of the lowest coefficients of friction of any solid material. It glides on PTFE as well as wet ice on wet ice. Moreover, the static friction is as high as the sliding friction, so that the transition from standstill to movement is smooth (non-stick-slip effect).
An impressive example of this was the 47.5 m movement of the new 12,500 tonne Oberkassel Bridge in Düsseldorf on PTFE sliding bearings on 7 and 8 April 1976 (link – in German). There are almost no materials that adhere to PTFE because the surface tension is extremely low.
PTFE is extremely resistant to all acids and bases, alcohols, ketones, petrol, oils, etc. and not resistant to sodium. In addition, PTFE is also frost resistant to -200 °C, can only be bonded after pre-treatment, physiologically harmless and non-flammable.
The inherent colour of the standard grades is opaque white. The service temperature range is up to approximately 260 °C. PTFE melts at 327 °C and also decomposes into highly aggressive hydrofluoric acid and highly toxic pyrolysis products.
PTFE has been used in furniture glides for several years. This is due to the unique combination of rubber and PTFE, which provides both excellent noise damping and optimum floor protection or minimal adhesive and sliding friction forces when furniture is moved.
The construction usually consists of a 2-3 mm flat, one-sided spherical rubber base (also square and rectangular shapes) to which a 1/10 mm thick PTFE film is applied under high pressure and temperature. These Universal Glide Inserts (UG) can be nailed, glued or inserted into wooden chair legs or other wooden furniture glides.
- Look in our range under the heading “Feet and glides” for the article series UG/RE, UG/RU, UGN/RU, GLUG, GGUG 2000 and KKSGUG.
PTFE glide inserts are recommended for easy movement of furniture on most floor coverings. They make it much easier to move furniture on carpeted floors. PTFE is not suitable for seating furniture on smooth floors, as it will slip unintentionally during use.
PU (PUR) – Polyurethane
PU is one of the most versatile plastics available. Depending on the formulation and manufacturing process, PU can be produced as a thermoplastic (TPU thermoplastic elastomer), elastomer or thermoset. We encounter PU products in all areas of daily life (mattresses, shoe soles, tyres for rollers and wheels, insulation panels, soundproofing elements, paints, adhesives, insulating foam and much more).
Look in our range under the heading “Divers small parts” for the article series UEP, EP, GUR, UKP/OV
SB – Styrene Butadiene (also impact polystyrene, PS-I)
SB (1.04-1.05 g/cm³) is a relatively light, amorphous thermoplastic. It is tough and has a much higher toughness than polystyrene (PS). It is not weather resistant. SB is mainly used (also foamed -> TSG) for low-cost housings and housing parts in the interior. The inherent colour is a very muted white (opaque white). SB is processed at around 180-280°C, is highly flammable, burns brightly and strongly sooty with a sweetish odour and a slight smell of burnt rubber.
- Look in our range under the heading “Electro accessories” nach der Artikelserie PCS, in der Rubrik “Operating elements/ control hardware” nach den Artikelserien VCF, VGF, DGA, DCA
Additives
Additives are substances that are added to the raw plastic to extend or improve its property profile and optimise its cost-benefit ratio. Typically, any plastic offered to processors on the market already contains several additives. In addition, there are additives that processors can add themselves or that experienced compounders can incorporate into their compounds. Additives can be broadly divided into the following groups according to their function:
Flame retardant
- to reduce the rate of fire or to achieve self-extinguishing – Verification e.g. by classification and registration by Underwriter Laboratories (UL).
Slip and processing aids
- can be divided into internal (e.g. to reduce friction/frictional heat during processing – zinc stearate and to adjust viscosity) and external (demoulding aids, friction reduction – oils, silicone, PTFE, MoS2, graphite).
Conductivity mediator
- to improve electron conductivity (metal threads, conductive carbon black, carbon fibres, etc.)
Impact resistance modifier
- to improve fracture resistance or to prevent crack rooting and to prevent crack propagation.
Finishing agents and brighteners
- to mask colour casts in natural coloured plastics caused by non-colour neutral additives or thermal pre-damage during production.
Stabilisers
- against heat, light (e.g. HALS* against UV damage) and other degradation attacks involving decomposition or chemical modification of the macromolecules (antioxidants, etc.).
*) = HALS ((Englisch –hindered amine light stabiliser) – do not absorb UV radiation, but inhibit polymer degradation by continuously and cyclically removing of radicals generated by photooxidation of the polymer
Compounds (composite material)
Compounds are ready-to-use material formulations in granular or powder form. They contain one or more plastics and, depending on the requirements profile, additives, colourants, fillers and reinforcing materials. Compounds for thermoplastics and thermoplastic elastomers are usually produced on adapted mixing extruders with subsequent pelletising. This results in a very material-friendly production with high homogeneity. Highly filled, high-viscosity compounds, e.g. for the production of ceramic or metal powder moulding compounds, where the plastics only act as a binder, are produced in mixing kneaders.
Colourings
The colouring of plastics is done by means of organic or inorganic colour or effect pigments, which are added to the plastics during processing or compound production in the processing variants
- powder colour
- liquid colour (with liquid carrier)
- pasty colour (with pasty carrier)
- colour masterbatch (colour granulate from pressed powder colour or colour granulate with low, mostly neutral plastic carrier content)
with usually 0.5-5%. If there are high requirements for colour matching of parts from different materials (plastics, metals, wood), paint manufacturers or compounders are usually responsible. However, the involvement of compounders or colour manufacturers usually leads to a considerable increase in the cost of the parts list components. The technical coordination of the colouring of different parts of the BOM is usually circumvented by choosing different colours for the parts of the BOM.
Filler materials
The fillers (additives) are usually inexpensive, cost-reducing substances that do not deteriorate the properties of the plastic through the addition or only in a controlled manner (wood flour, etc.).
Reinforcements
Reinforcements give stressed plastic components or semi-finished products better stiffness, higher mechanical strength and higher heat resistance. Embedded reinforcements in the form of fibres, fabrics, spheres and grains made of glass, carbon, plastic and minerals are used, some of which, with adhesion promoters and an aligned embedding, enable even additional strength increases. Intrinsic reinforcements by stretching fibres, e.g. of polyamide and polyethylene, are also possible.
Blends
Blends (polymer blends) are generally understood to be mixtures of two or more different thermoplastics. No new chemical bonds of the molecules are formed, but purely physical blends are present. This is only possible with the help of a chemical adaptation, as thermoplastics are usually not compatible with each other (destruction, segregation or delamination) or adhesion is only possible by spraying one thermoplastic onto another in the mould. The properties of the resulting plastics differ greatly from the original plastics. Known blends are PA+ABS, PC+ABS, PC+PET, PC+PBT.
Macromolecules
Macromolecules contain a large number of atoms chemically linked by principal valences and, according to Staudinger, are divided into linear molecules and spherical molecules or plastics depending on the degree of polymerisation (hemicolloids – degree of polymerisation 10 to 100, mesocolloids – degree of polymerisation 100 to 500 and eucolloids – degree of polymerisation > 500).
Monomers
Monomers are low-molecular, reactive single molecules of plastics and have at least one functional group (reactive or bonding group as a prerequisite for bonding in polymers).
Homopolymere und Copolymere
Homopolymers are polymers that consist of only one type of monomer. They have only one repeating unit.
Copolymers (also called heteropolymers) are polymers (chemical substances made of macromolecules) that are built up from two or more different monomer units. In the production process, the product properties can be specifically controlled.
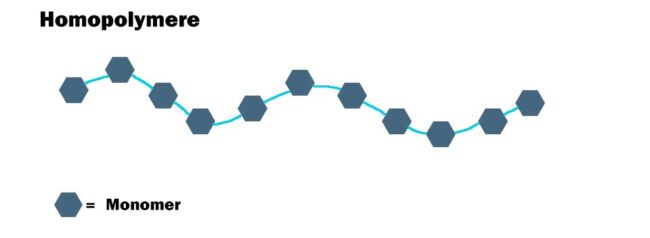
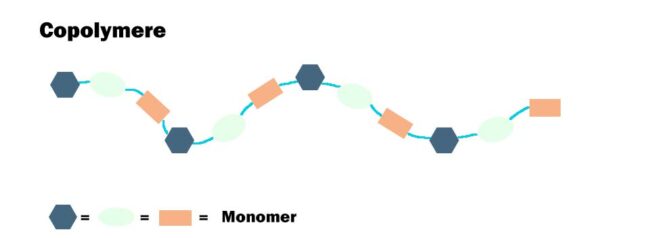
Polymers or plastics are produced by polymerisation, polyaddition or polycondensation (is specific to the type of plastic). Depending on the degree of polymerisation, they contain a corresponding number of main valency-bound monomers. Plastics are classified according to their (main) chains in terms of chain length differences between molecularly narrow or widely distributed and according to their molecular weight between low and ultra-high molecular weight.
Amorphous and semi-crystalline
Thermoplastics are divided into amorphous and semi-crystalline.
- In amorphous thermoplastics, the atoms do not form an ordered structure but show a disordered pattern. Amorphous structures are usually transparent as glass.
- In semi-crystalline thermoplastics, both chemically regular and geometric areas form. There are therefore areas where crystals form. Crystallites are parallel bundles of molecular segments or folds of molecular chains. Single chain molecules can partially penetrate into the crystalline or the amorphous region. Sometimes they can even belong to several crystallites at the same time. Partially crystalline structures lead to a translucent to opaque intrinsic colour.
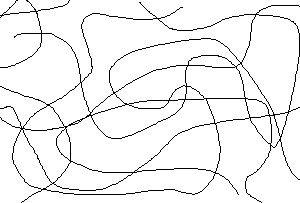
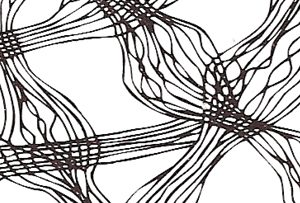
Tacticity
The arrangement of the side chains on the main chains of the macromolecules essentially determines the properties of the plastics (amorphous or semi-crystalline and thus crystal-clear-transparent or translucent to opaque inherent colour, chemical resistance, mechanical values, etc.). A distinction is made between:
- atactic – the side chains are unevenly arranged
- isotactic – the side chains are arranged uniformly on one side
- syndiotactic – the side chains are evenly alternated
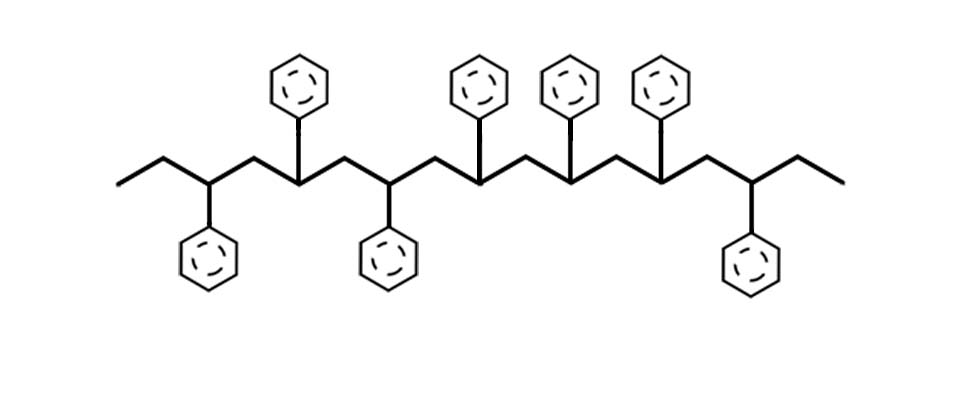
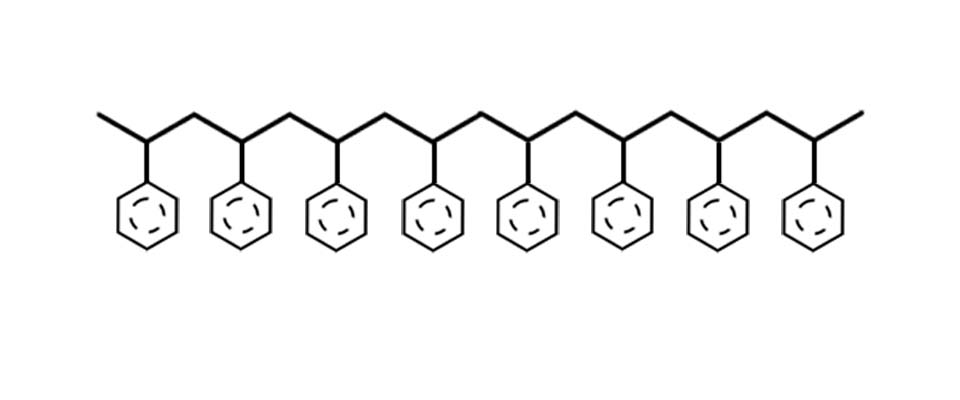
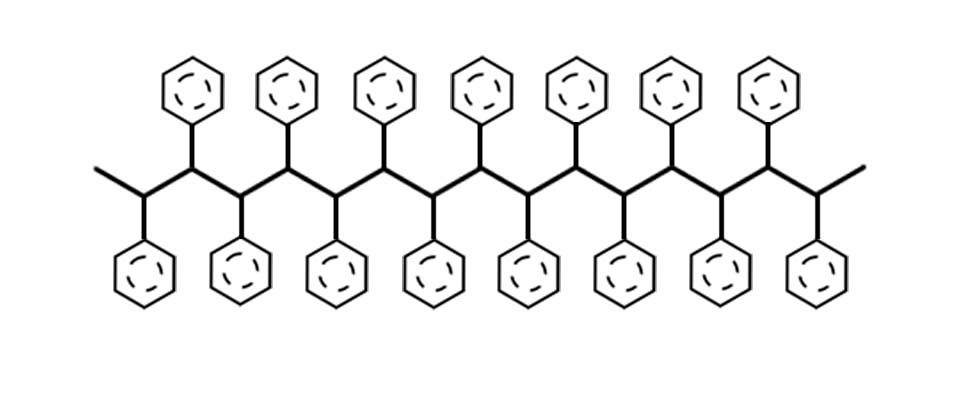